AWARDS FINALIST: Fryer heat recovery cuts fuel use
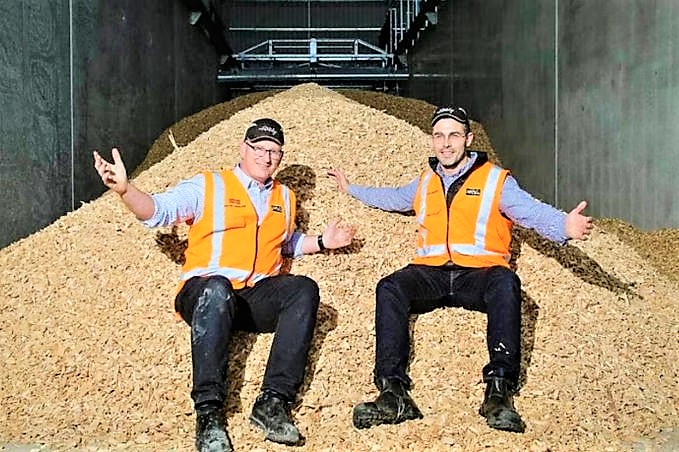
McCain Foods’ Energy Transition Accelerator programme for its Timaru plant has helped forge a pathway to reduce its process heat demand and enable it to switch its boiler fuel to renewables.
A key part of that programme was to capture energy from the frying process which would otherwise be lost to the atmosphere, and use it to supply energy to other upstream processes.
Collaborating initially with Waikato University and then with De Kleijn Consultants, McCain – the world’s leading producer of prepared potato products and appetisers – designed a fryer heat recovery system working on the concept of heat recovered by open cycle heat pump.
Heat recovery system
French fries are par fried in a bath of oil at 175˚ C, which reduces the moisture content by up to 15 per cent.
Normally, this moisture would be evaporated to the atmosphere in the form of vapours. Instead, energy from the high temperature fryer exhaust vapours is recovered and is used to heat a closed loop water supply which is then flashed under vacuum pressure inside the flash tank using mechanical vapour recompression or MVR.
The steam is used in a heat exchanger to heat other upstream processes previously done using direct steam injection. The condensate produced flows back to the flash tank and is then pumped to a plate heat exchanger – which pre-heats the boiler feed water to 65˚C – before returning to the fryer vapour condenser.
Challenges
One of the technical challenges the project team encountered was the requirement for the vapofan/MVR to work continuously – the supplier recommended no more than three stops in a 24-hour period. To avoid a low steam inflow rate – a major cause of potential stoppages – the team installed a bypass valve connecting the fan outlet to the inlet, ensuring the mass flow remained above the minimum required.
A delay in the delivery of vapofans from Germany saw the project team make the decision to commission the system in 2 phases. Phase 1 – commissioning the boiler feed water heat recovery – took place during the annual shutdown, while phase 2 – commissioning the blancher heat recovery – followed a couple of months later, when the vapofans were delivered.
Other challenges included design changes due to it being the first such project for everyone on the team; the Ukraine war; steel supply shortages; and Covid-19.
Broader application
The vapofan/MVR installed at McCain is the first of its kind in New Zealand for its specific type of heat recovery application. It is highly likely that this application of MVR technology is a global first.
According to the supplier there are a few factories that have deployed MVRs for heat recovery around the world, but McCain is the first to use a vapofan integrated operating monitoring (OPM) system.
The heat recovery system installed by McCain can be replicated easily in any industry across the globe. Any facility having low grade waste heat can use vapofans or MVRs depending on their heating requirements. In New Zealand, where the emissions from electricity uptake is minimal, this technology is a very efficient solution.
Benefits
From McCain’s perspective, the project has proved very successful and has helped it move a step closer to its 2030 goal of a 50 per cent reduction in carbon dioxide emissions.
The system is exceeding its design parameters, and is currently recovering around 1743 kW of energy from the fryer vapour compared to 1510 kW.
The project will help the plant reduce its energy usage by 39,943 gigajoules a year, or 3946 tonnes of carbon emissions - while burning sub-bituminous coal. It will also help the site cut water consumption by 17,600 cubic metres a year, in turn lowering the amount of chemicals needed to treat the feedwater.
The installation of vapofans, pumps and an exhaust fan is set to increase electricity consumption by 1.48 GWh a year, however the plant’s net energy savings are estimated to be around 11.09 GWh a year.
The plant’s monthly energy monitoring report shows an 8 per cent drop in energy intensity with respect to monthly production volume compared to the previous year.
The Large Energy User Initiative of the Year category is sponsored by EECA