AWARDS FINALIST: Alsco Uniforms – Coal-free five years early
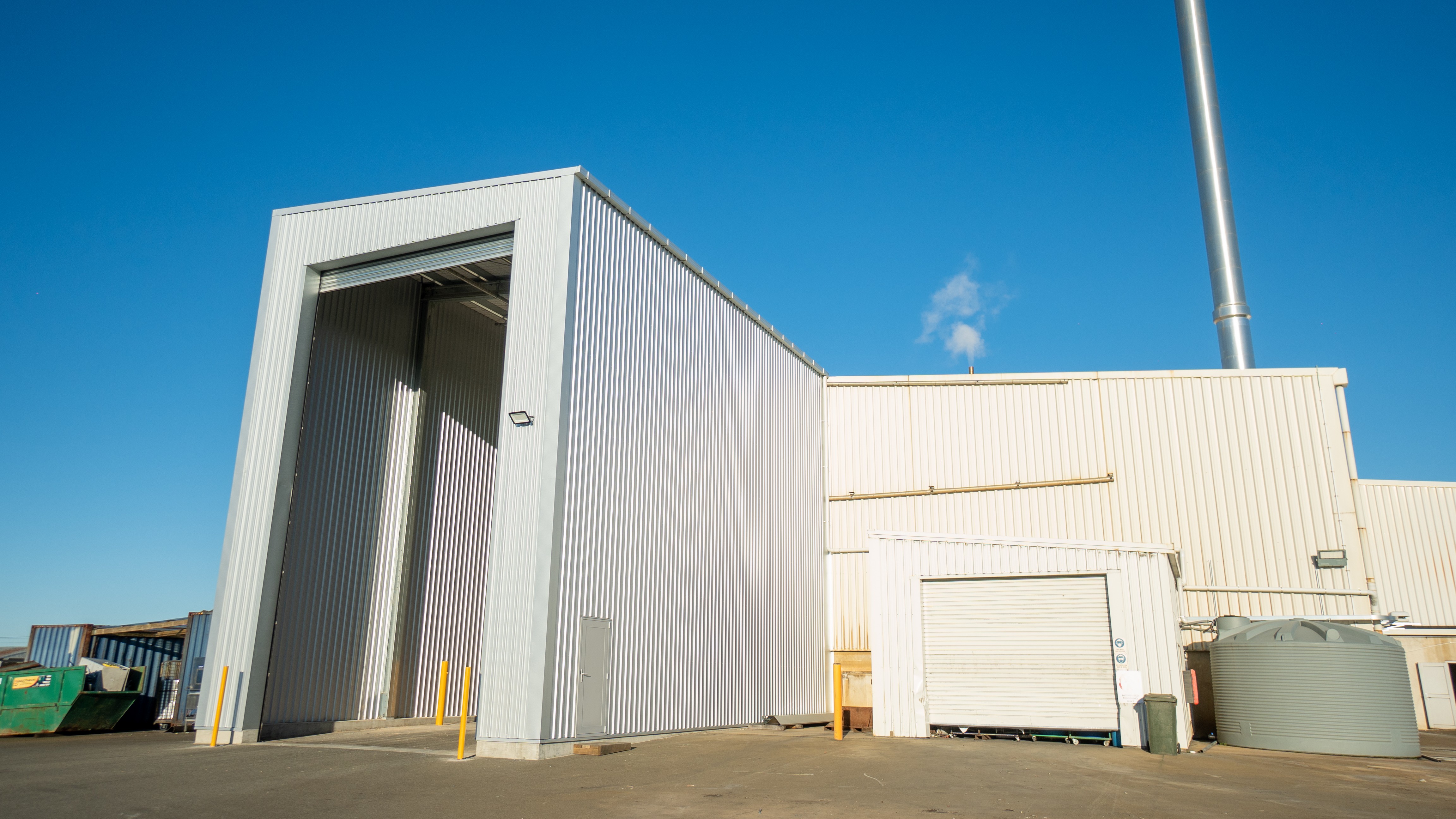
Alsco Uniforms has shifted its operations away from coal five years ahead of its 2030 target.
The conversion of the Christchurch and Invercargill facilities to biomass last year completed that transition, bringing the group's total emissions reduction to 60 per cent of its 2019 baseline.
This achievement places Alsco Uniforms well ahead of national targets and the emissions goals set by the Science Based Targets initiative.
Alsco Uniforms' journey began with a bold decision. Faced with an ageing 50-year-old 4.8 megawatt coal boiler at its Christchurch facility, the company could have opted for a $300,000 re-tube.
Instead, it chose to invest in a new $3.4 million biomass boiler, supported with co-funding from the Energy Efficiency and Conservation Authority's Government Investment in Decarbonising Industry Fund.
Wood pellets
The new 3.5 MW Vekos Firetube boiler, manufactured locally by MHM Automation, runs on wood pellets and delivers consistent, high-efficiency steam - cutting emissions by the equivalent of 1990 tonnes of CO₂ a year.
In Invercargill, based on earlier trials, Alsco Uniforms opted to retrofit the fuel storage and handling system, including weatherproofing biomass storage of its existing 4.5 MW Vekos boiler at a cost of $347,000.
This enabled the boiler to run on wood pellets instead of lignite coal and lifted the boiler efficiency from 77 per cent to 82 per cent. The result is 4075 tonnes of CO₂ avoided each year.
The conversions, both assisted with EECA funding, were not without challenges. Installing the Christchurch unit required careful safety planning and design work to remove the plant's roof and crane the boiler in over neighbouring properties.
New consents were required, as were temporary boilers and fuel silos to maintain operations while the new plant was brought online.
Alsco Uniforms says the benefits extend beyond emission reductions.
Clean environment
Staff at the Invercargill site now work in a cleaner, quieter environment, free from coal dust and soot. Maintenance downtime has dropped, steam pressure is more stable and production has increased. The transition has also eliminated the need for frequent boiler cleaning.
Alsco Uniforms says its approach was as much about local impact and innovation as it was about reducing carbon emissions.
By choosing New Zealand-made equipment and working with local contractors - MHM Automation for boiler construction and Kelford Engineering for decommissioning, installation and commissioning - the company supported regional economies and built national capability in biomass technology. Alsco also contracted Core Steel Building, a local Invercargill-based civil engineering firm, for the construction of the new fuel storage facility in a bid to support the local Southland economy.
The decision to avoid importing European systems reduced supply chain risks and demonstrated that world-class decarbonisation can be achieved with homegrown solutions.
Commercially, Alsco Uniforms says the move positions it as a sustainability leader in the industrial laundry sector. While operational costs have increased slightly, the company says the costs are far outweighed by the long-term benefit of reduced emissions, improved efficiency and alignment with customer values.
The annual Energy Excellence Awards will be held in Wellington on 13 August. The Large Energy User Initiative of the Year Award is sponsored by EECA.